022Cr19Ni10
發(fā)布時(shí)間:2020/03/24 點(diǎn)擊量:
022Cr19Ni10
圓鼎金屬
〓〓〓〓〓〓上海圓鼎歡迎您〓〓〓〓〓〓〓〓
022Cr19Ni10化學(xué)成分:
022Cr19Ni10介紹:
022Cr19Ni10是為解決304材料的Cr23和C6析出致材料在一些條件下存在嚴(yán)重的晶間腐蝕傾向而發(fā)展的超低碳奧氏體不銹鋼。其敏化態(tài)耐晶間腐蝕能力顯著比304好,除強(qiáng)度稍低外,其它性能和304一樣??梢杂猛ㄓ玫母鞣N不銹鋼焊接工藝焊接,焊接后可以不進(jìn)行熱處理。
◆◆◆◆◆◆◆◆◆◆◆◆◆◆◆◆◆◆◆◆◆◆◆◆◆◆◆◆◆◆◆◆◆◆◆◆◆◆◆
022Cr19Ni10應(yīng)用和特性:
022Cr19Ni10應(yīng)用領(lǐng)域:主要用于化工、石化、化肥、石油、動(dòng)力等工業(yè)需焊接后又不能固溶處理的設(shè)備、容器、管道及各種沖壓零部件。
022Cr19Ni10材質(zhì)規(guī)格:
冷拉棒 6-14熱扎棒10~100mm,線材0.5-30,鍛制棒:100mm~350mm,冷扎薄板0.05mm-4.0mm,熱扎板:4mm~14mm,帶2mm-10mm,壓延版0.05-2.0,各尺寸規(guī)格鍛件環(huán)件,上海圓鼎金屬定尺、定制、庫(kù)存。個(gè)別牌號(hào)不定尺。
022Cr19Ni10物理性能:
022Cr19Ni10標(biāo)準(zhǔn)下力學(xué)性能:
圓鼎小知識(shí)(固溶作用):
①鋼中合金碳化物的析出與溶解
鋼中C是所含合金元素之一,其除能起到一點(diǎn)強(qiáng)化作用之外,對(duì)耐蝕性是不利的,特別是C與Cr形成碳化物時(shí),作用更壞,應(yīng)力求減少它的存在。為此,依據(jù)C在奧氏體中隨溫度不同而變化的特性,即在高溫時(shí)溶解度大,低溫時(shí)溶解度小。有資料報(bào)導(dǎo),C在奧氏體中的溶解度在1200℃時(shí)為0.34%;1000℃時(shí)為0.18%,而600℃時(shí)為0.02%,室溫時(shí)則更少。所以將鋼加熱到高溫,使C-Cr化合物充分溶解,再快速冷卻,讓其來(lái)不及析出,保證鋼的耐蝕性,特別是耐晶間腐蝕性。
②σ相
奧氏體鋼如果在500-900℃區(qū)間長(zhǎng)時(shí)間加熱,或鋼中加入Ti、Nb、Mo等元素時(shí),都會(huì)促進(jìn)σ相析出,使鋼增加脆性和降低耐蝕性,消除σ相的手段也是在高于其可能析出溫度使其溶解,再快速冷卻,防止再析出。
工藝:
在GB1200標(biāo)準(zhǔn)中,推薦加熱溫度范圍較寬:1000~1150℃,通常采用1020-1080℃??紤]具體牌號(hào)成分,是鑄件還是鍛件等情況,在允許范圍內(nèi),適當(dāng)調(diào)節(jié)加熱溫度。加熱溫度低,C-Cr碳化物不能充分溶解,溫度太高,也存在晶粒長(zhǎng)大,降低耐蝕性問(wèn)題。
冷卻方式:應(yīng)以較快速度冷卻,防止碳化物再析出。在我國(guó)及其它一些國(guó)家標(biāo)準(zhǔn)中,標(biāo)明固溶化后“快冷” ,綜合不同文獻(xiàn)資料和實(shí)踐經(jīng)驗(yàn),“快”的尺度可按如下情況掌握:
• 含C量≥0.08%的;含Cr量>22%、Ni量較高的;含C量雖<0.08%,但有效尺寸>3mm的,應(yīng)水冷;
• 含C量<0.08%、尺寸<3mm,可風(fēng)冷;
• 有效尺寸≤0.5mm的可空冷
022Cr19Ni10加工處理和焊接性能:
022Cr19Ni10是碳含量較低的304不銹鋼的變種,用于需要焊接的場(chǎng)合。較低的碳含量使得在靠近焊縫的熱影響區(qū)中所析出的碳化物減至最少,而碳化物的析出可能導(dǎo)致不銹鋼在某些環(huán)境中產(chǎn)生晶間腐蝕(焊接侵蝕)。優(yōu)異的冷加工性能,及良好的焊接性能,焊后無(wú)需熱處理。適用各類焊接工藝。
〓如有不盡之處可撥打上海圓鼎熱線詳細(xì)咨詢〓〓
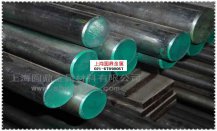
圓鼎金屬
〓〓〓〓〓〓上海圓鼎歡迎您〓〓〓〓〓〓〓〓
022Cr19Ni10化學(xué)成分:
碳C | 硅Si | 錳Mn | 磷P | 硫 S | 鉻Cr | 鎳Ni |
0.030 | 1.00 | 2.00 | 0.045 | 0.030 | 18-20 | 10-12 |
022Cr19Ni10是為解決304材料的Cr23和C6析出致材料在一些條件下存在嚴(yán)重的晶間腐蝕傾向而發(fā)展的超低碳奧氏體不銹鋼。其敏化態(tài)耐晶間腐蝕能力顯著比304好,除強(qiáng)度稍低外,其它性能和304一樣??梢杂猛ㄓ玫母鞣N不銹鋼焊接工藝焊接,焊接后可以不進(jìn)行熱處理。
◆◆◆◆◆◆◆◆◆◆◆◆◆◆◆◆◆◆◆◆◆◆◆◆◆◆◆◆◆◆◆◆◆◆◆◆◆◆◆
022Cr19Ni10應(yīng)用和特性:
022Cr19Ni10應(yīng)用領(lǐng)域:主要用于化工、石化、化肥、石油、動(dòng)力等工業(yè)需焊接后又不能固溶處理的設(shè)備、容器、管道及各種沖壓零部件。
022Cr19Ni10材質(zhì)規(guī)格:
冷拉棒 6-14熱扎棒10~100mm,線材0.5-30,鍛制棒:100mm~350mm,冷扎薄板0.05mm-4.0mm,熱扎板:4mm~14mm,帶2mm-10mm,壓延版0.05-2.0,各尺寸規(guī)格鍛件環(huán)件,上海圓鼎金屬定尺、定制、庫(kù)存。個(gè)別牌號(hào)不定尺。
022Cr19Ni10物理性能:
熔點(diǎn)/℃ |
比熱容 /kg/(kg.k)℃ 100~900℃ |
熱導(dǎo)率/w/(m.k) 100~500℃ |
線脹系數(shù) /(10-6/k) 100~500℃ |
密度g/cm | 磁性 |
1398-1420 | 0.5 | 16.3-21.5 | 16.8-18.3 | 7.96 | 無(wú) |
標(biāo)準(zhǔn)號(hào) | 熱處理 | 硬度(不大于) |
拉伸強(qiáng)度Σb\MPa ≥ |
延伸率A/% ≥ |
斷面收縮Z/%≥ |
GB/T1220-2007 | 固溶 |
187HBW 90HRB |
480 | 40 | 60 |
①鋼中合金碳化物的析出與溶解
鋼中C是所含合金元素之一,其除能起到一點(diǎn)強(qiáng)化作用之外,對(duì)耐蝕性是不利的,特別是C與Cr形成碳化物時(shí),作用更壞,應(yīng)力求減少它的存在。為此,依據(jù)C在奧氏體中隨溫度不同而變化的特性,即在高溫時(shí)溶解度大,低溫時(shí)溶解度小。有資料報(bào)導(dǎo),C在奧氏體中的溶解度在1200℃時(shí)為0.34%;1000℃時(shí)為0.18%,而600℃時(shí)為0.02%,室溫時(shí)則更少。所以將鋼加熱到高溫,使C-Cr化合物充分溶解,再快速冷卻,讓其來(lái)不及析出,保證鋼的耐蝕性,特別是耐晶間腐蝕性。
②σ相
奧氏體鋼如果在500-900℃區(qū)間長(zhǎng)時(shí)間加熱,或鋼中加入Ti、Nb、Mo等元素時(shí),都會(huì)促進(jìn)σ相析出,使鋼增加脆性和降低耐蝕性,消除σ相的手段也是在高于其可能析出溫度使其溶解,再快速冷卻,防止再析出。
工藝:
在GB1200標(biāo)準(zhǔn)中,推薦加熱溫度范圍較寬:1000~1150℃,通常采用1020-1080℃??紤]具體牌號(hào)成分,是鑄件還是鍛件等情況,在允許范圍內(nèi),適當(dāng)調(diào)節(jié)加熱溫度。加熱溫度低,C-Cr碳化物不能充分溶解,溫度太高,也存在晶粒長(zhǎng)大,降低耐蝕性問(wèn)題。
冷卻方式:應(yīng)以較快速度冷卻,防止碳化物再析出。在我國(guó)及其它一些國(guó)家標(biāo)準(zhǔn)中,標(biāo)明固溶化后“快冷” ,綜合不同文獻(xiàn)資料和實(shí)踐經(jīng)驗(yàn),“快”的尺度可按如下情況掌握:
• 含C量≥0.08%的;含Cr量>22%、Ni量較高的;含C量雖<0.08%,但有效尺寸>3mm的,應(yīng)水冷;
• 含C量<0.08%、尺寸<3mm,可風(fēng)冷;
• 有效尺寸≤0.5mm的可空冷
022Cr19Ni10加工處理和焊接性能:
022Cr19Ni10是碳含量較低的304不銹鋼的變種,用于需要焊接的場(chǎng)合。較低的碳含量使得在靠近焊縫的熱影響區(qū)中所析出的碳化物減至最少,而碳化物的析出可能導(dǎo)致不銹鋼在某些環(huán)境中產(chǎn)生晶間腐蝕(焊接侵蝕)。優(yōu)異的冷加工性能,及良好的焊接性能,焊后無(wú)需熱處理。適用各類焊接工藝。
〓如有不盡之處可撥打上海圓鼎熱線詳細(xì)咨詢〓〓
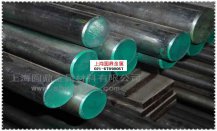
> Inconel686 ?? ? 2024-05-20
> HastelloyC22 ?? ? 2024-05-20
> HastelloyC4/哈氏合金 ?? ? 2024-05-20
> HastelloyC276/哈氏合金 ?? ? 2024-05-20
> HastelloyC加工與焊接 ?? ? 2024-05-20
> HastelloyB3 ?? ? 2024-05-17
> MonelK500機(jī)械強(qiáng)度對(duì)比Mo ?? ? 2024-05-17