SKD1耐磨性
發(fā)布時間:2021/08/18 點擊量:
SKD1
SKD1合金元素冶煉的影響:
一、SKD1材料介紹:
SKD1相當于ASTM A681中D3鋼,具有良好的耐磨性,適宜制作受沖擊負荷較小的要求較高耐磨的沖模及沖頭、冷剪切刀、鉆套、量規(guī)、拉絲模等。
二、SKD1材料用途:
SKD1適宜制作受沖擊負荷較小的要求較高耐磨的沖模及沖頭、冷剪切刀、鉆套、量規(guī)、拉絲模等。
五、SKD1化學成分:
SKD1合金元素冶煉的影響:
合金成分碳:C增加淬火組織的硬度;形成碳化物,提高耐磨性;降低韌性;降低可焊性鉻:Cr提高鋼之硬度,形成堅硬及穩(wěn)定的碳化鉻,從而改善耐磨性;能提高鋼的淬透性;當Cr含量超過12%, 具耐腐蝕作用,并提供良好拋旋光性鉬:MoMo是強碳化物形成元素,提高耐磨性;Mo>0.5%能抑制其他合金元素引致之回火脆性;提供紅硬性,熱強度;提高淬透性,回火穩(wěn)定性釩:V可以形成高硬度碳化物,提高耐磨性;細化鋼的晶粒,降低過熱敏感性提高鋼之強度、韌性及回火穩(wěn)定性鎳:NiNi能提高鋼的淬透性;Ni能細化晶粒硫(S)常以MnS形式存在鋼中,割裂基體的連續(xù)性,惡化材料的韌性、抗腐蝕性、拋旋光性、放電加工性、蝕紋性,可提高材料的切削能力。2. 冶煉工藝普通煉鋼工藝電渣重熔(ESR)將粗鋼坯置于電渣爐中,通入強電流,使電爐產(chǎn)生很高的溫度,使粗鋼坯熔化成鋼水,鋼水流經(jīng)電渣,雜質(zhì)被電渣過濾吸附,從而達到純化的效果。整體重熔速度快,但一些非常細小的雜質(zhì)并未除去。真空電弧重熔(VAR)在真空爐里,通入強電流在鋼胚上,鋼胚底部開始熔化,雜質(zhì)汽化成氣體被抽走,從而將鋼材純度提高,而且它是一滴一滴地凝固,凝固速度非???,組織變得很致密。特點是雜質(zhì)去得徹底,但整體重熔速度慢。3. 熱處理鋼材的熱處理是指經(jīng)過加熱然后冷卻,通過控制鋼材的加熱溫度、保溫時間及冷卻速度來改變鋼鐵性能,以滿足加工或使用要求的工藝過程。主要的熱處理工藝有:退火、淬火、回火、固溶時效。
一、SKD1材料介紹:
SKD1相當于ASTM A681中D3鋼,具有良好的耐磨性,適宜制作受沖擊負荷較小的要求較高耐磨的沖模及沖頭、冷剪切刀、鉆套、量規(guī)、拉絲模等。
二、SKD1材料用途:
SKD1適宜制作受沖擊負荷較小的要求較高耐磨的沖模及沖頭、冷剪切刀、鉆套、量規(guī)、拉絲模等。
五、SKD1化學成分:
碳C | 硅Si | 錳Mn | 磷P | 硫 S | 鉻Cr |
2.00~2. 30 | ≤0. 40 | ≤0. 40 | ≤0. 030 | ≤0. 020 | 11.5~13 |
SKD1材料加工難點分析,主要有以下幾個方面:
1)SKD1切削力大,切削溫度高: 材料強度大,切削時切向應力大、塑性變形大,因而切削力大。此外材料導熱性極差,造成切削溫度升高,且高溫往往集中在刀具刃口附近的狹長區(qū)域內(nèi),從而加快了刀具的磨損。
2)SKD1奧氏體組織切削時加工硬化傾向大,通常是普通碳素鋼的?刀具在加工硬化區(qū)域內(nèi)切削,使刀具壽命縮短。
3)SKD1容易粘刀。無論是奧氏體還是馬氏體均存在加工時切屑強韌、切削溫度很高的特點。當強韌的切屑流經(jīng)前刀面時,將產(chǎn)生粘結(jié)、熔焊等粘刀現(xiàn)象,影響加工零件表面粗糙度。
因此SKD1的生產(chǎn)制造過程中應控制好以下兩點:
1)提高SKD1的純凈度,降低不銹鋼材料基體中夾雜物的含量。
2)改善成分設計及熱、冷軋退火工藝,降低不銹鋼材料基體中δ鐵素體的含量。
但由于SKD1在生產(chǎn)過程中不可避免地會存在此兩種制造缺陷,因此在保溫杯等制品加工過程中也可采取適當?shù)墓に嚧胧﹣頊p輕或避免由夾雜物或δ鐵素體缺陷導致的開裂現(xiàn)象:
1)將成形方式由減薄拉深改為等厚拉深。
2)增加拉深道次,增大凹模圓角半徑,降低材料的變形難度。
3)適當增大拉深油的黏稠度,促進材料均勻變形,避免應力過于集中、SKD1物理性能: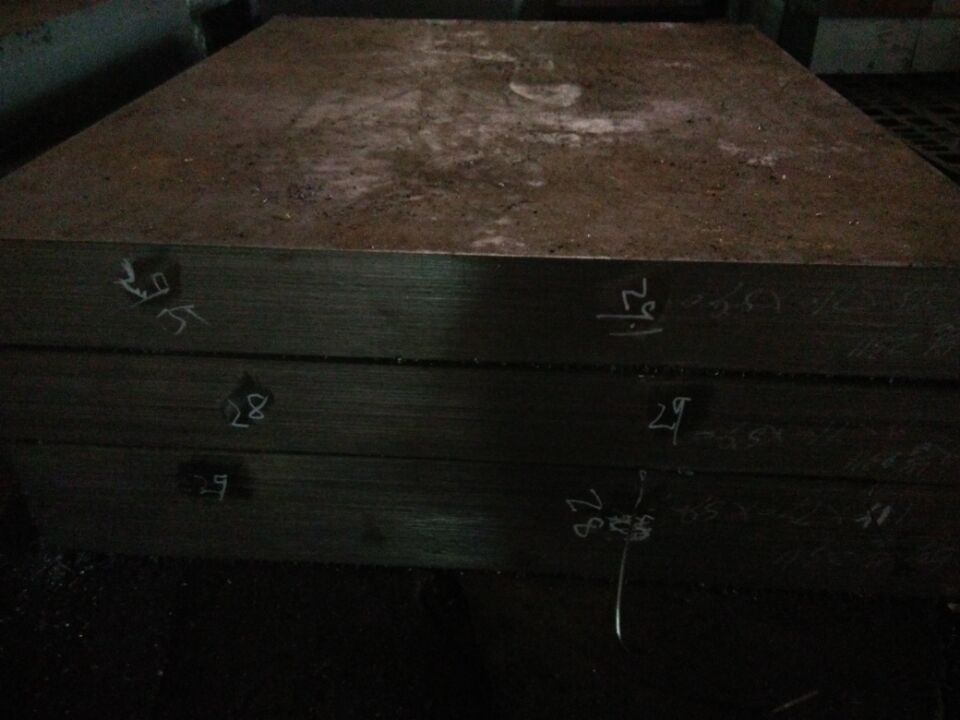
g/cm³ | 硬度 |
拉伸強度Σb\MPa |
延伸率A/% |
斷面收縮Z/% | |
HBW217~269 |
> No6022 GH高溫合金/Incon ?? ? 2022-05-19
> DTD5026 GH高溫合金/Inco ?? ? 2022-05-19
> 68Ni28Cu28Al GH高溫合金 ?? ? 2022-05-19
> No5500 GH高溫合金/Incon ?? ? 2022-05-19
> N05500 GH高溫合金/Incon ?? ? 2022-05-19
> 2.4374 GH高溫合金/Incon ?? ? 2022-05-19
> 2.4375 GH高溫合金/Incon ?? ? 2022-05-19